Calibration is a central element of many functioning quality systems and is an important process for a Quality Manager or Engineer. It becomes a routine task on varying frequencies and is an accepted part of the quality system, but it is important that we understand why it is done and remind ourselves of the significance of it and the possible implications if we don’t do it or are late in doing it.
What is calibration?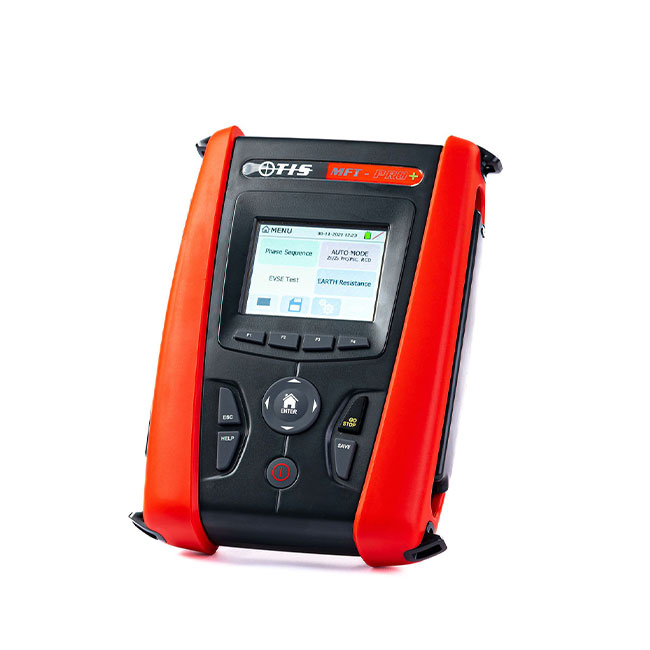
When a device is used it can start to lose accuracy over time and measurements can start to drift. This is known as a measurement error, and is the difference between the measurement value of quantity and the true value. Calibration therefore is the comparison between a measurement standard and the measurement being given by the instrument, to determine what the error is, if there is one, and to establish what adjustments have to be made to the instrument to ensure it is 100% accurate to the standard.
Some instruments may never show these measurement errors, but you need to check them all the same to prove this, and as such, the calibration process creates documented traceability to prove that calibration has been done and accuracy can be assured. Other instruments, perhaps those used more frequently or in harsh environments, may show this error more often, or at least the deviations from standard might become so great that they are no longer within a specification, and therefore you can no longer assure accuracy and quality.
It can be agreed that calibration is the act of determining and documenting this measurement error and recording it. If the error is outside a permissible range then adjustments will be made to the device, to reconfigure it so that deviations from the measurement specification are minimised. In many cases this process will involve an element or repair and maintenance of a device, but this may also fall under a separate planned preventive maintenance process.
Why do we calibrate?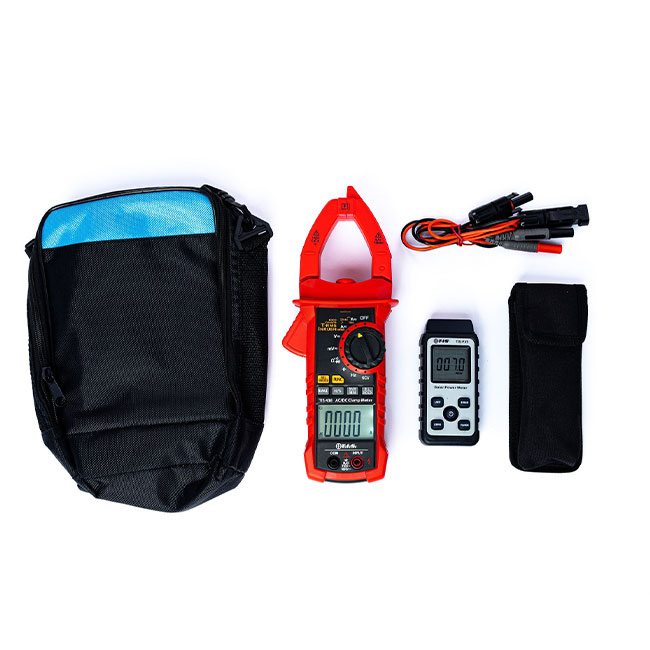
Different industries have different operating and controlling standards, and different organisations also have different internally and externally-controlled quality systems, and the calibration of instruments is done to ensure compliance with these standards.
To many operators and users it may appear that calibration is merely a check to ensure an instrument is reliable and its measurements can be trusted, and while this is true, to the business, calibration carries lots of responsibilities and safeguards against varying implications.
There are many potential costs a business can face if they fail to calibrate instruments, are using instruments ‘out of calibration’ or are knowingly recording measurements and relying on measurements which are possibly not accurate, at least within an acceptable error range. These costs could include:
- Legal costs – claims and product liability from product failures or health and safety failures
- Non-compliance costs – international standards/UK standards or internal quality systems
- Business relationships and reputational damage
- Repairs due to failures caused by incorrect measurements
When should we calibrate?
Instruments can show a measurement error for many different reasons, it can be because of normal wear and tear of the instrument, because of electrical or mechanical shock or damage to the instrument or because it is being used in a hazardous environment. All these factors need to be considered when assessing a calibration frequency. But this frequency may also be determined by a quality standard you are operating under. There are many different safety standards involved in electrical testing or in the food industry, for example – where high standards of health and safety are critical - so to comply with these standards, the standard may dictate that you have to calibrate your instruments within a set frequency. The specifications of your internal quality systems may also have a set frequency, and the manufacturing spec of the instrument itself may also have a recommended calibration frequency.
In general, however, unless you are controlled by an external standard, an organisation should carry out a risk assessment of the instrument to determine the implications of possible inaccuracy. Ultimately, you need to have confidence that the measurements your instrument is giving are accurate. In some cases inaccuracy of measuring may result in system failure or product failure that could cause injury, death, health and safety or environmental breaches and certainly non-compliance with a standard, so wherever this kind of measurement is necessary, calibration is an essential element of your operating procedures.